在福建福清核電站這片工業熱土上,我國具有完全自主知識產權的核電“國家名片”——“華龍一號”正平穩地運行著。
其中長約21米、重達390噸、直徑約4.6米的龐然大物——“華龍一號”ZH-65型蒸汽發生器,被工匠們親切地喚作“核電之肺”。
它不僅是“華龍一號”中安全級別最高、最為核心的設備之一,更是中國核電技術自主創新的璀璨明珠,承載著無數東方電氣人的夢想與希望。

▲國產首臺“華龍一號”蒸汽發生器
從“0”到“1”繪就自主制造壯麗畫卷
回望來時路,“華龍一號”的誕生,是中國核電技術從跟跑到并跑,再到領跑的華麗轉身。在這充滿荊棘與挑戰的過程中,蒸汽發生器的設計與制造難度,如同一場攀登珠穆朗瑪峰的極限挑戰。
“3000多個零件,5800多根傳熱管,17000多條焊縫……”時任項目設總鄧智勇的內心既激動又憂慮。他知道,這些數字是對每一位參與者耐心與毅力的極限考驗,這不僅是一項技術任務,更是一次國家使命的擔當。
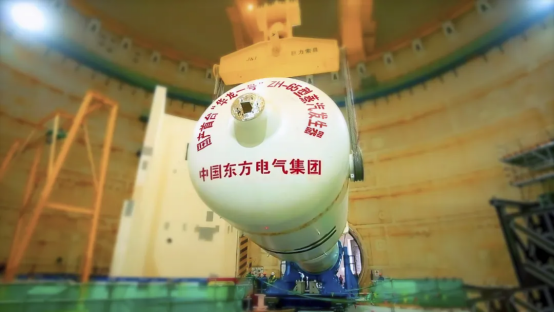
根據交貨工期安排,福清5號機組首臺蒸汽發生器計劃2017年完工交貨,第二、三臺蒸汽發生器交貨期相距僅差1個月。要保證“華龍一號”首堆質量和安全,蒸汽發生器研制必須攻克技術關、質量關、進度關。
面對技術封鎖、時間緊迫的重重困難,東方重機的項目團隊成員迅速集結,成立“華龍一號”蒸汽發生器攻關小組,夜以繼日地投入到這場沒有硝煙的戰斗中。
在那段日子里,車間的燈火常常徹夜不熄,工程師們的身影在其間穿梭不息。
每一張圖紙,都凝聚著他們的心血與智慧;每一條焊縫,都見證著他們的汗水與堅持。正是這份對技術的執著追求,對國家的深沉熱愛,讓東方電氣人在逆境中找到了前進的方向,在挑戰中書寫了屬于自己的輝煌篇章。
自主創新突破核心技術壁壘
“每一步都充滿了未知與挑戰,但正是這些困難,鑄就了我們自主創新、勇攀高峰的精神。”面對“華龍一號”蒸汽發生器較之二代改進型的顯著變化——更復雜的制造技術,更嚴苛的質量管控,鄧智勇帶領的團隊沒有退縮,而是選擇了迎難而上。
管板,這一蒸汽發生器的核心部件,其厚重與精密令人嘆為觀止。600毫米的合金鋼身軀,承載著11670個直徑精確至17.73毫米、垂直度要求0.45毫米的管孔,如同浩瀚宇宙中的繁星點點。
“我們要做的,不僅僅是制造,更是創造。”鄧智勇清楚記得,設備制造之初,遇到技術瓶頸,想過找國外合作伙伴來共同解決技術問題,但碰了“軟釘子”。
“一定要突破關鍵核心的制造技術!”他與攻關團隊心里憋著一股勁。
走訪調研、引入國產新設備、計算機數值模擬分析、工藝試驗驗證……攻關組的成員們一點點攻克著深孔加工的各項難題。
“陷入瓶頸的時候,連續一個月都住在公司,有時候半夜來了靈感,抓住同事就開始討論。”回憶那段時光,參與者都覺得干勁滿滿。
核電設備國產化道路上,需要攻克的“卡脖子”技術很多,三葉梅花孔拉削工藝、已加工孔檢測的間歇式推掃觸發攝影測量技術、局部熱處理防DING(凹痕)技術......這些晦澀的技術術語,正是今天“華龍一號”蒸汽發生器輝煌成就的點滴印證。
核級匠心守護國之重器
如果說蒸汽發生器是核電站的靈魂,那么焊接工藝就是其生命力的源泉。
在制造“華龍一號”國內首臺ZH-65型蒸汽發生器的過程中,焊接人員遇到了前所未有的挑戰。多處結構焊接后產生的裂紋,如同一道道鴻溝,橫亙在他們面前。
面對這一難題,手工焊接組組長游科沒有選擇退縮。他深知,核電安全容不得半點馬虎。于是,他與團隊毅然決然地投入到長達一個月的焊接實驗中。無數次的嘗試與失敗,無數次的挫折與堅持,終于找到了原因——焊接過程受氣流影響導致焊縫缺陷、原料焊接性能差、焊道排布不合理影響焊縫質量。
明確癥結,精準施策。攻關團隊憑借著豐富的經驗和過人的智慧,鉆研出了相應的焊接方法,成功攻克了這一質量難題。
然而,勝利的果實并非輕易可得。在蒸汽發生器的心臟——管束組件的制造過程中,李堅和他的搭檔面臨著更為艱巨的任務。

▲管束組-穿管
5800多根管子、11670個管孔、管壁厚度僅有1毫米……為了確保穿過9層支撐板時的一次合格,他們借助激光對準儀,眼神交匯間,以同樣的力道、同樣的速度,甚至同樣的呼吸節奏來完成這一高難度的操作。
當最終聽到一次合格的消息時,游科和李堅等人的臉上露出了久違的笑容。
2021年1月30日,福建福清核電5號機組完成滿功率連續運行考核,投入商業運行,標志著國產首臺“華龍一號”ZH-65型蒸汽發生器的性能指標達到合同要求,中國核電技術走在世界前列。
從巴蜀腹地到灣區之心,東方重機肩負核電裝備國產化、自主化歷史使命,將繼續以東汽精神為坐標,服務國家戰略,鑄就絕對安全的“國之重器”,用東方力量推動實現中國式現代化。